You’re handed a headset and told to stand within a square marked off on the floor with tape. After lowering the headset over your eyes, you’re no longer in the training room. You’re in a BNSF mechanical shop, standing on the walkway of an orange locomotive.
A friendly BNSF employee stands in front of you. She greets you and walks you through a detailed training program. Before you know it, you’re reaching out and grabbing digitally generated tools, reading instructions that are hovering in front of you, following a complex procedure to change out parts inside the engine. You’re also wondering what you look like to anyone watching from outside your little bubble as you gesture animatedly with your arms and hands.
You’re experiencing virtual reality (VR) training in a mechanical environment. Virtual reality, which may be most familiar as an immersive way to play games using consumer headsets, also has many industrial applications.
Christopher Skinner, locomotive mechanical manager, has played a leading role in the implementation of VR training at BNSF.
“BNSF is always striving to be innovative and lead the industry, and that also carries over into our training department,” Skinner said.
One of the big reasons BNSF chose to deploy VR training within the mechanical arena is consistency. “You have control of a standardized method of delivering training,” Skinner said. “With instructor-led training, the message can vary depending upon the instructor and location, so there’s a possibility of losing critical information.” With VR training, mechanical students receive precisely the same information across the company.
Skinner said deploying the technology was a massive undertaking because of the volume of information that had to be compiled to build the mechanical training courses digitally. His role is to act as liaison between BNSF and the project vendor.
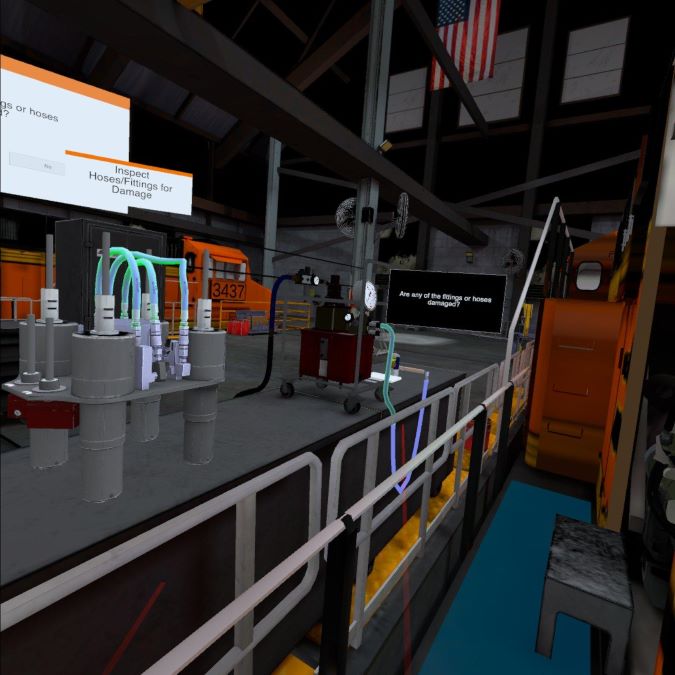
Building a VR environment requires rendering many objects in 3D. “We had to build models and make sure they looked accurate and had the level of detail that we needed – anything from the locomotive to the shop environment to individual components and tooling,” Skinner said.
In many cases, where a digital equivalent of a tool or part didn’t exist, the experts within the BNSF Technical Training Center had to make one. “We really had to kind of reverse-engineer the locomotive to build the components that we needed,” Skinner said. “We’d obtain the physical component and take multiple photos from different angles, with a tape measure or ruler for perspective.” With that information, the digital component was created.
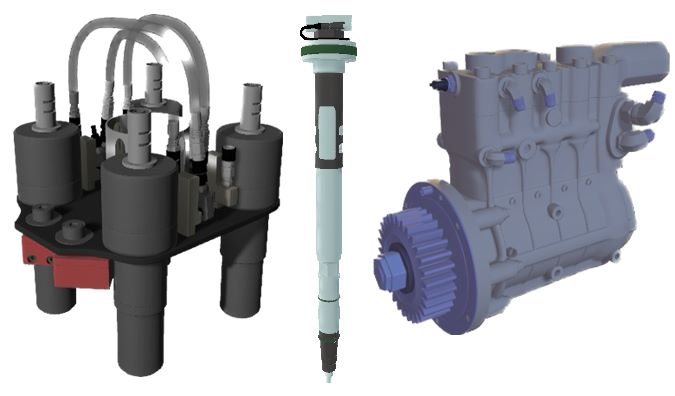
“Sometimes we’d get permission from a mechanical shop to disassemble parts of a non-production locomotive to take photos and measurements, and we’d also take videos of the process,” Skinner said. “So instead of trying to explain to the vendor what the exact process was, the video could show the process we’re trying to replicate.”
Much of the work of modeling the digital parts was performed by Bill Snyder, senior specialist for railroad training. The advantages of working in a digital environment had been on Snyder’s mind for some time.
“Kids coming up nowadays love their video games, and people learn very easily with video games,” Snyder said. “I would love to have our training set up where you can just give it to the students and let them go in and explore the environment. I want to have a training environment that engages our students and makes them want to be in it, so when you tell the student they’ve got five more minutes to finish, they’re asking for five more minutes or another half hour because they don’t want to stop.”
After more than two years, BNSF has eight VR mechanical training modules, all covering maintenance processes for Tier IV locomotives. This type of locomotive has significantly reduced emissions and is compliant with the latest U.S. Environmental Protection Agency emissions standards. These modules include three safety briefings, fuel pump installation and removal, injector installation and removal, and specialty tooling tension/de-tension processes.
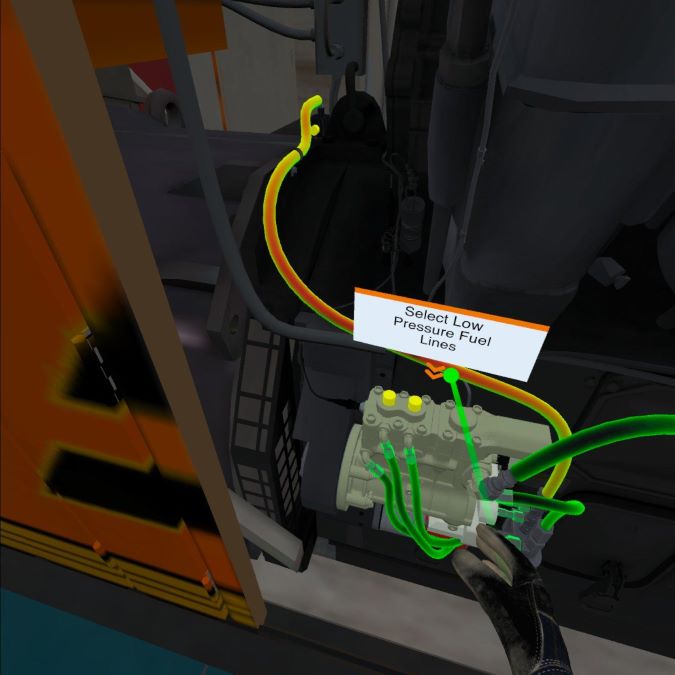
“We’ve now implemented mechanical VR training in the field and our plan is to have folks who attend our Tier IV instructor-led training class go through the VR material first before they perform the process in reality,” Skinner explained.
That’s important for safety. For example, there are mechanical maintenance processes that involve working with equipment under thousands of pounds of pressure. A deviation from the correct procedure could potentially result in injury. A potential alternative is to master the process virtually.
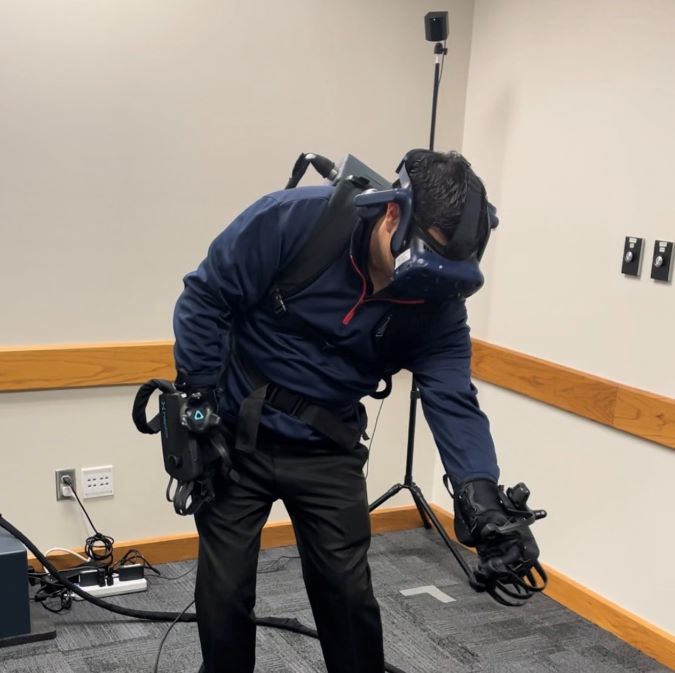
“You can literally practice these processes dozens of times inside this virtual reality environment until you’re familiar and comfortable with them,” Skinner said. “And then you can go and safely implement them in real life.”
The experience of working in a virtual environment may be disorienting at first, and it takes practice grasping and manipulating the 3D-rendered tools and parts. Still, most employees adapt well to the new training. “We have had very few cases where folks just don’t grasp it,” Skinner said. There is a desktop version employees can use if they don’t take to the virtual environment.
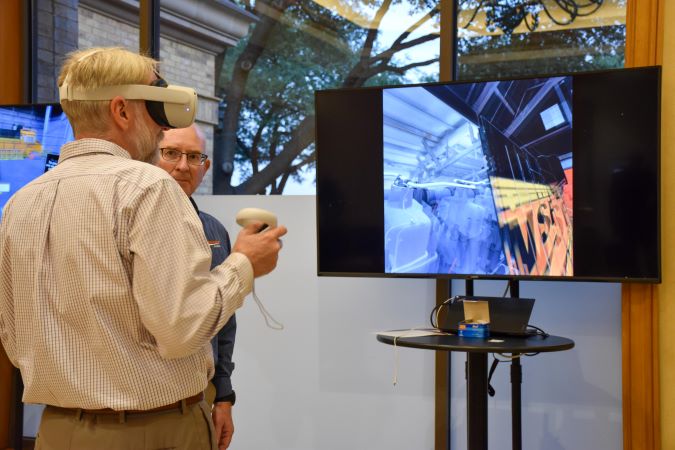
Looking ahead, he sees the potential for continued investment in the technology, including acquiring more headsets to be permanently available at multiple work locations around the network.
“We’re also looking at adding haptic gloves,” Skinner said. “You get real-life resistance to your hands to make it feel like you’re picking up items, which adds to the realism of the training.”
Over time the range of coursework available will potentially expand. “The dream is that we have a large library spanning across various departments and crafts,” he said.
The implementation of VR mechanical training is expected to aid locomotive availability and reduce service interruptions, ultimately benefiting the company and its customers. Safety, efficiency, consistency, and immediate availability of training, regardless of location: The training might be virtual, but the benefits are very real.
Quelle: