What capabilities do industrial metaverses have, and how do manufacturers leverage them?
The topic of the metaverse generated a lot of hype, especially after Facebook Inc. had rebranded into Meta Platform Inc. to reflect the company’s purpose in building the full-fledged metaverse. And while the metaverse is strongly associated with social and entertainment in the collective consciousness, this breakthrough technology has much broader potential. It can drive value to enterprises in various industries.
Manufacturing is one sector that can benefit significantly from the metaverse. Mass implementation of such solutions has even distinguished a manufacturing-specific branch of this ecosystem called the industrial metaverse. So what capabilities do industrial metaverses have, and how do manufacturers leverage them? As a metaverse development company, we know the answers from firsthand experience.
What is the Industrial Metaverse?
The industrial metaverse definition implies the implementation of the metaverse for the manufacturing, construction, and engineering sectors that create a virtual, highly immersive virtual environment for specialists to collaborate remotely or build simulations.
One of the primary building blocks of the industrial metaverse ecosystem is digital twins. This technology allows the creation of identical virtual copies of particular physical objects, systems, or processes. However, a digital twin is more than a simple duplicate. The difference is that a digital twin is linked to its physical counterpart and receives real-time updates. The convergence of the metaverse and digital twinsfacilitates the precise integration of real-life entities like equipment and machinery into the virtual dimension, ensuring that any manipulation will correspond with how things are in reality.
The Evolution of the Industrial Metaverse
Modern manufacturing and related sectors are going through the Fourth Industrial Revolution, a rapid level-up of the processes, approaches, and mechanics brought by the development of profound innovations, namely smart automation. The key technologies that drive change include the Internet of Things (IoT), artificial intelligence, machine learning, advanced robotics, 3D modeling, and others.
So what about the metaverse? Is humanity going through the metaverse industrial revolution right now? While the metaverse trends are gaining popularity, we must catch up to its mass implementation. The high-level concept of the metaverse implies the existence of a fully-fledged virtual dimension that users can easily explore through virtual avatars. This requires advanced interconnectivity, robust and scalable infrastructure, as well as the widespread adoption of VR/AR/MR devices, and we still need to reach such a state.
As for now, the metaverse looks like a set of separate virtual dimensions instead of an interconnected virtual world. In the industrial environment, most enterprises only start to explore the full capabilities of the metaverse, transferring merely some processes there. However, some market leaders adopt industrial metaverse solutions faster. They show that it’s possible to create full-scale factories in the virtual dimension and remove physical barriers and limitations, creating a vision for the future path of industrial metaverse development.
Industrial Metaverse Market Size
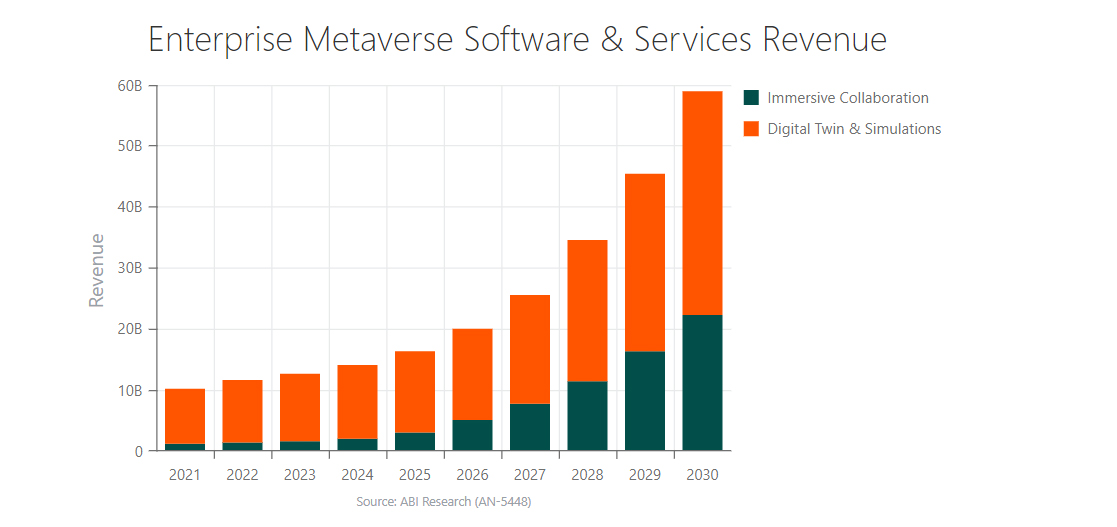
The industrial metaverse market is built on immersive collaboration and digital twins/simulations, and according to researchers, the revenues from these aspects are predicted to reach $58.9 bn by 2030. At the same time, the enterprise metaverse market is splintered, as most companies that offer metaverse-based solutions set up their standards and regulations. Therefore, there is a problem of lack of interoperability, creating a challenge for further market growth. The answer would be the standardization that will be initiated and adopted by the industry players.
The True Value of Industrial Metaverse
Even in the relatively early stages of its formation, the industrial metaverse can drive change and reinvent most processes. The implementation of the industrial metaverse allows the optimization workflow, as well as the transition from reactive to preventive or predictive approaches.
The metaverse empowers precise simulations, making it possible to do any manipulation with virtual counterparts of real-world entities without dealing with physical limits or risking jeopardizing system performance. Thanks to this, it’s possible to enhance production speed, ensure a higher quality and lower amount of defective products, optimize expenses, prolong equipment life, increase safety, and relieve employees from mundane, repetitive tasks. Overall, the metaverse paves the road for the rise of virtual factories that will transform manufacturing beyond recognition.
Industrial Metaverse Use Cases
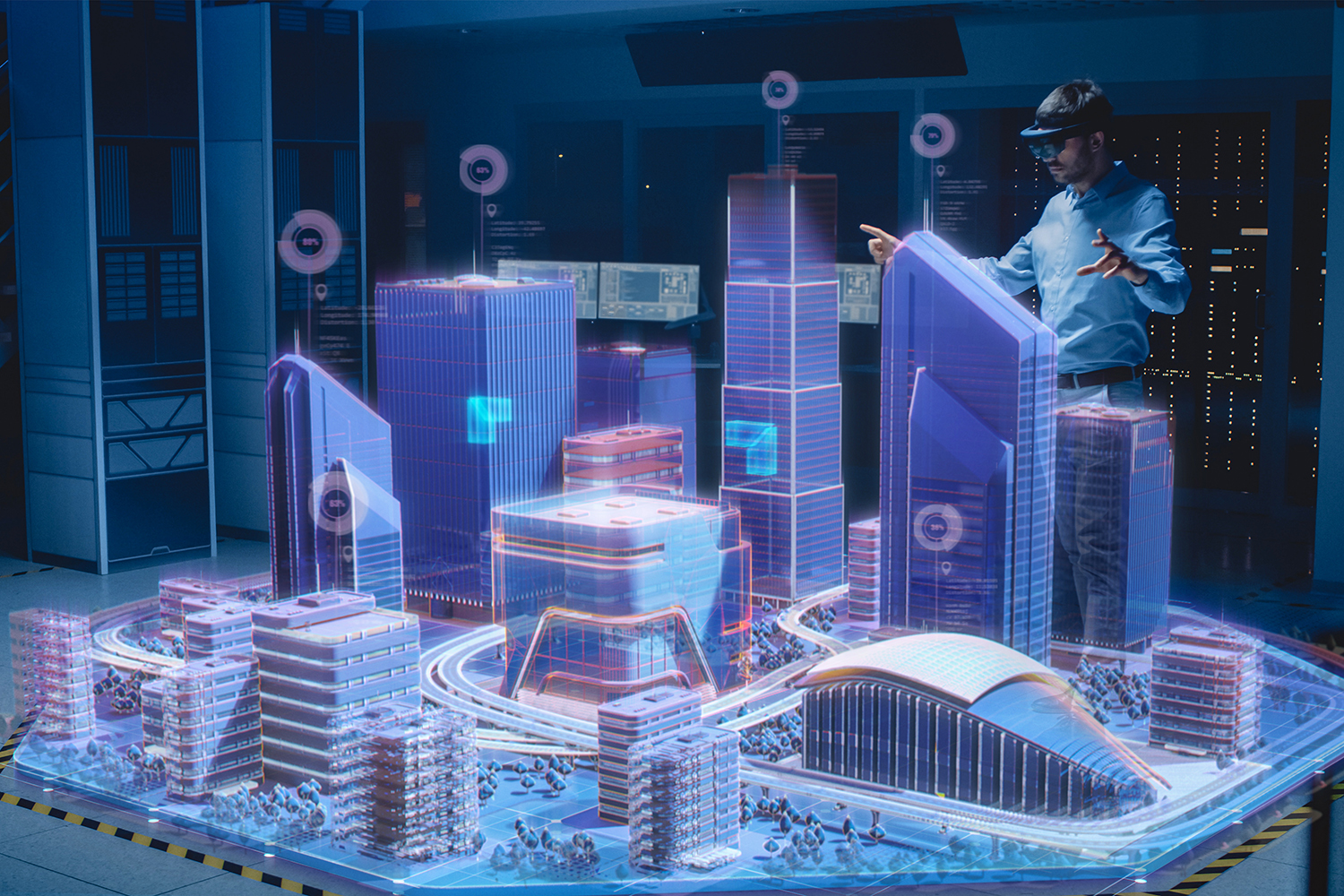
The metaverse use cases in the industrial sector vary and cover a lot of processes that occur on-site. Market leaders push the sector innovations forward as they show readiness to dedicate their investments to technological updates of their factories, equipment, hardware, or software. Here are a few examples of how manufacturers leverage metaverse and related technologies to improve workflow.
1. Employee Training in the Metaverse
Using the metaverse expands training and education capabilities, making it more accessible, safe, and efficient than the traditional approach. Therefore, increasingly, companies have decided to leverage VR and simulation to teach their employees the necessary skills, submerge them into real-life conditions without jeopardizing their safety, and remove physical barriers that might create obstacles to smooth collaboration and learning.
First, manufacturers can create identical virtual copies of equipment or heavy machinery to introduce new employees in a controlled, accident-free environment. It also increases the quality of the training, as trainees get a chance to study a piece of equipment in and out, which might be impossible in real life.
Second, metaverse training empowers immersive hazardous scenarios training. Instead of conducting a simple briefing, safety instructors can simulate dangerous situations and go through the actual cause of actions with employees. This way, employees can acquire fundamental skills to act in hazardous conditions and remember them during an accident.
Third, the metaverse allows the creation of a 3D model virtual database of equipment or other items. They can be available for any employee at any time of the day, so specialists can deepen their knowledge and skills whenever needed without disrupting the production process or requiring the assistance of other team members.
2. Virtual Collaboration in the Metaverse for Designing or Maintenance
The precise simulation reinvents traditional approaches to product design and facility maintenance. Through the metaverse capacities, specialists don’t need to figure out the issues or resolve challenges on the go when operating with physical entities. Real-life objects can be easily replaced with digital copies, and manipulating any virtual object is much easier than a real one.
In terms of product design, implementing the metaverse means giving out physical prototyping and moving to the virtual dimension, which demands fewer resources and where your testing capacities are much broader. Maintenance also becomes more efficient because manufacturers can monitor the state of equipment in real-time and predict breakages before they happen, therefore applying preventive measures.
Another significant benefit is remote collaboration. The metaverse exists in the virtual dimension, and users can access it anywhere. Hence, remote specialists or invited experts don’t need to travel miles to visit your factory or plant on-site: they can put on a VR set and find themselves in a virtual copy of your facility. And with high simulation accuracy, experts accessing you through the metaverse will be able to perform at the same level as they would if visiting in real life.
3. Metaverse-powered Virtual Simulation for Optimization
Digital twins, a core technology for the industrial metaverse we have already mentioned, enable advanced optimization for manufacturers. A digital twin goes beyond simulating a single object: a business can build a set of duplicates and simulate a production floor, a whole department, or even a whole factory. While testing different scenarios with their help, businesses can detect bottlenecks, systems‘ weak spots, and other issues that slow down growth or waste resources, taking appropriate measures in real-life to remove any obstacles.
At the same time, specialists can use digital twins to do a trial testing of their improvement hypothesis to see how they will impact the entire system. This evaluation will help understand the practicality of suggested optimization and avoid dedicating investments, time, and human efforts to an idea doomed to fail from the start.
4. Introduction of Virtual Designs Created in the Metaverse
Besides incorporating changes into internal processes, the metaverse can transform the relationship between businesses and customers. The physical and virtual borders become thinner, so manufacturers can use this to create new revenue streams.
Virtual designs are one of the mechanics of how this concept might work. When entering the metaverse, clients can create their designs of the brand’s product, whether a pair of shoes, a furniture set, or even something more substantial, like a detail for a particular vehicle. Then, a manufacturer will build this product and ship it to the customer, who will receive a product customized by their own hands.
Tap into the Industrial Metaverse with the Help of Program-Ace
The industrial metaverse promises a lot to manufacturers who dare to explore such innovative technologies. This technology has already started to revolutionize manufacturing, putting the metaverse enthusiast in the lead, and the future looks even brighter for those businesses that are not afraid to break the barriers between physical and virtual.
Quelle: